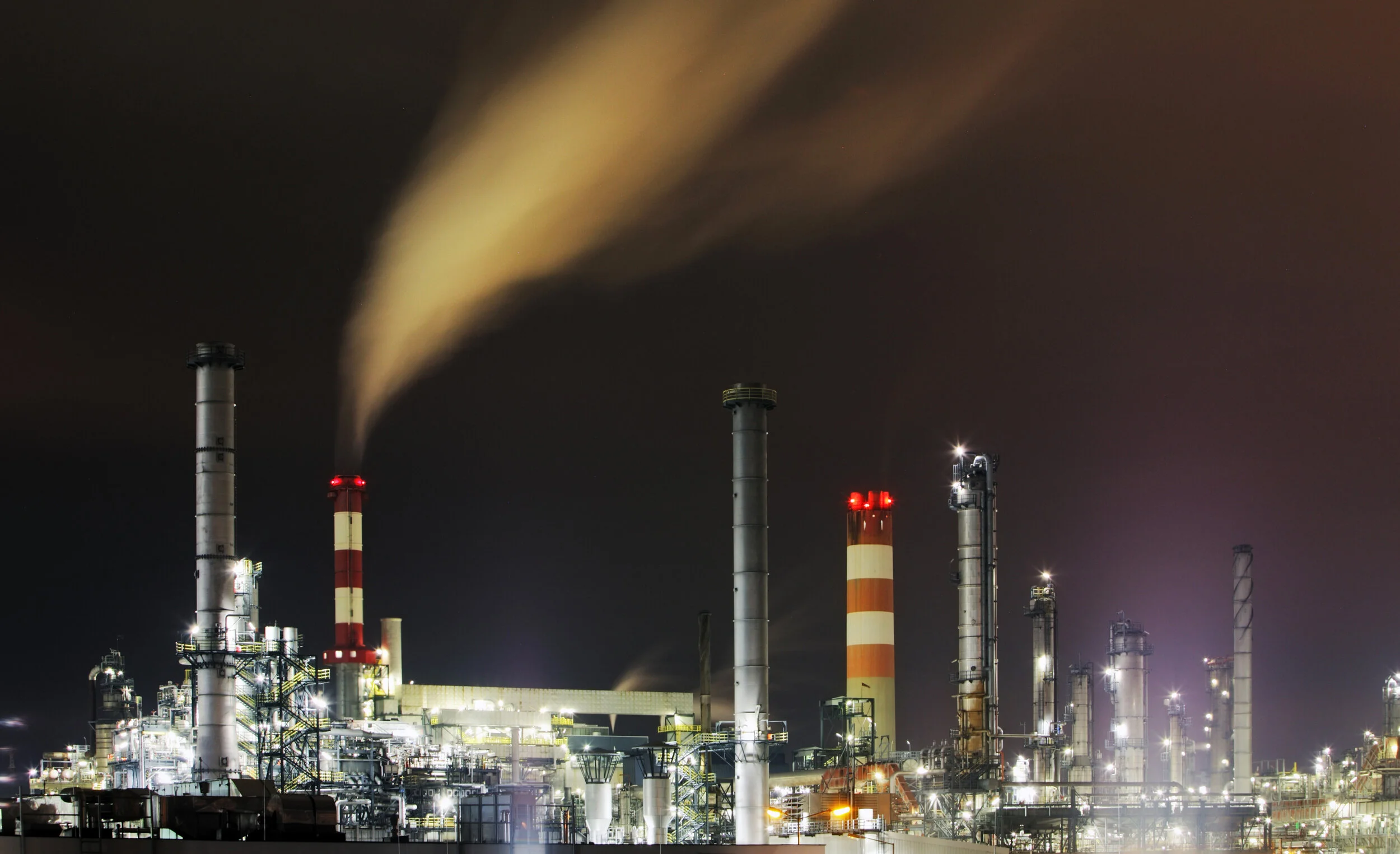
CHEMICAL MIXING
& INSPECTION
THE SITUATION
An international paint manufacturer stores indoor and outdoor facilities, thousands of totes of chemicals used to make paint. Teams of forklift operators must locate the correct totes of chemicals to combine for certain types and colors of paint and then stage them for the mixer. Much time is involved in locating the correct tote of each chemical to ensure the proper combination is achieved in the final product.
Colors and textures of paint chemicals are not discernable to the eye, so operators rely on barcode identification numbers to select the correct chemicals. Locating the exact number of each vat of chemicals is a painstaking, lengthy manual process. Any mistake in selecting the inputs could result in an incorrect batch that must be destroyed, resulting in wasted time and materials.
The company must also keep up with regulatory mandates that require routine inspections on all equipment. Inspectors currently do inspections with pen and paper and then upload information to a server when they return to their office, meaning inspections may take hours or days to complete.
The company is seeking a solution that will simplify the process of locating and inventorying the correct chemicals. They also want a simpler digitized process for inspecting their equipment in order to meet regulatory mandates.
THE CHALLENGE
The chemicals used in paint mixing are highly toxic and . The areas where these chemicals are stored and mixed are classified as hazardous locations because the chemicals are highly combustible. Thus, any electronic equipment used in these areas, including any computing devices, must be officially certified “intrinsically safe” for UL Class I Division 1 hazardous areas, where flammable materials are constantly present. Intrinsically safe equipment is designed to not be capable of causing a spark that could potentially ignite an explosion.
REQUIREMENTS
The company is seeking a mobile solution that will improve the efficiency and accuracy of paint mixing. They also want a solution that would make inspections quicker and easier by completing the data entry onsite. The company would like its crew to be able to:
• easily identify and locate correct chemical totes
• quickly match chemical totes to the appropriate paint mixers
• verify the accuracy of each mix
• report inspection data onsite
• communicate in real time during mixing and during inspections
• visually share and discuss any issues
To perform these functions, crew members and inspectors need a mobile device that is specially certified for UL Class I, Division 1 areas, plus appropriate software applications that allow them to complete these tasks in real time.
THE SOLUTION
The proposed technology solution for this paint manufacturer is the Aegex10 Intrinsically Safe Tablet in conjunction with Snively Inc.’s TagMinder Intelligent RFID Automation software and Safety Tracker software. Using the Aegex10 IS Tablet, factory workers can employ TagMinder to verify that the barcodes of each chemical used in paint mixes are the correct ones, thereby guaranteeing an accurate mix, as well as helping operators save time when searching for the correct inputs.
To ensure all equipment is performing optimally, and to verify the safety and quality of their equipment, the paint manufacturer will also use Snively’s Safety Tracker software that allows for onsite digital inspection reporting. All of this is possible in real time in UL Class I Division 1 hazardous areas with the intrinsically safe Aegex10 IS Tablet.
HARDWARE
Using the Windows-based Aegex10 IS Tablet, operators can access Windows 10 apps, cloud services and third party apps, even in the most volatile hazardous areas (UL Class I,II,III Div 1; ATEX/IECEx Zone 1).
Certified for UL Class I, II, III Division 1 hazardous locations, as well as equivalent areas in Europe (ATEX Zone 1) and internationally (IECEx Zone 1), the Aegex10 operates on Wi-Fi or 4G LTE from any hazardous location around the globe on a unified platform. The 10.1-inch Aegex tablet is rated IP65 rugged for industrial use, yet is lightweight and priced as low as non-certified devices. Its Windows 10 operating system gives users uniform access to the Microsoft cloud, plus apps and services, including software like that of Snively.
“The Aegex10 IS Tablet is the basis for a true Internet of Things for the most hazardous zones of industrial operations.”
–Thomas Ventulett, Aegex CEO
“The Aegex + TagMinder solution has solved a huge problem for companies striving to guarantee the accuracy and quality of their product. It is also saving them time, which means better productivity.”
— Justine Blank, Strategic Business & Solution Architect, Snively Inc.
SOFTWARE
Snively Inc., a U.S.-based application developer and provider of hazardous area equipment, web apps, barcoding and RFID solutions, can provide the paint manufacturer with two separate pieces of software, TagMinder and Safety Tracker, to be used on the Aegex10 IS Tablet. Tagminder is an RFID-optimized inventory management solution that tracks items’ unique RFID tags, providing information about their movement and location. Users can integrate TagMinder with PLCs, back-end systems and shop floor systems. TagMinder also connects with external visual aids and triggers, such as light stacks, message boards, alarms, infrared beams, scales, etc., to allow automated and error-proof tracking of:
• Raw Materials
• Work-in-Process
• Finished Goods
• Machinery
• Reusable Containers
• Material Handling Equipment
• Consumables
• Human Assets
Safety Tracker is mobile inspection tool for hazardous area equipment. Specific inspection instructions are generated when an inspector scans the barcode or RFID tag of each piece of equipment. The inspector can complete the inspection onsite on an approved mobile device that is communicating directly with a centralized database on the company’s network or can be synchronized to a database once connected.
THE RESULTS
With the Aegex10 IS Tablet and Snively software, forklift operators can enter the most volatile hazardous areas (UL Class I, II, III Division 1) and more easily locate the correct totes of chemicals to be used in paint mixing without fear of causing an explosion.
Using the Aegex tablet and Snively TagMinder, workers can:
1. Scan the barcode of each tote of paint
2. Scan the work cell of the paint pump
3. Pass the data over Wi-Fi or 4G LTE from TagMinder on the tablet to a programmable logic controller (PLC)
4. Verify with the PLC that the correct combination of ingredients is being selected
5. Send an affirmative or negative response to the tablet from the PLC
6. If the proposed mixture is correct, the PLC automatically starts the pump. If it is incorrect, the tablet operator can easily locate the correct inputs by using TagMinder to find the correct product on the tablet.
Using the Aegex tablet and Snively Safety Tracker, inspectors can:
1. Scan the barcode or RFID tag of each piece of equipment with the Aegex10 IS Tablet
2. View automated inspection scripts for each asset
3. Check off each inspection item on the tablet screen
4. Store resulting data for each inspection in the Safety Tracker log and/or automatically upload it to a server for online storage and sharing.
With the Aegex10 IS Tablet, operators can also use a number of Windows 10 applications to communicate information to teammates, such as:
• Opening a Skype for Business line to speak directly and show visually the item in question
• Using Exchange/Outlook to email photos or other data
• Uploading information to a Microsoft cloud-based platform
The Snively apps can be used anywhere in hazardous locations via the Aegex10 IS Tablet. Certain apps are also viewable offline when wireless networks are not available. The solution is transferrable across different geographies since the Aegex10 IS Tablet is certified worldwide.
The Aegex10 IS Tablet + Snively solution reduces mistakes in the manufacturing process and makes inspections simpler and quicker, even in hazardous areas.