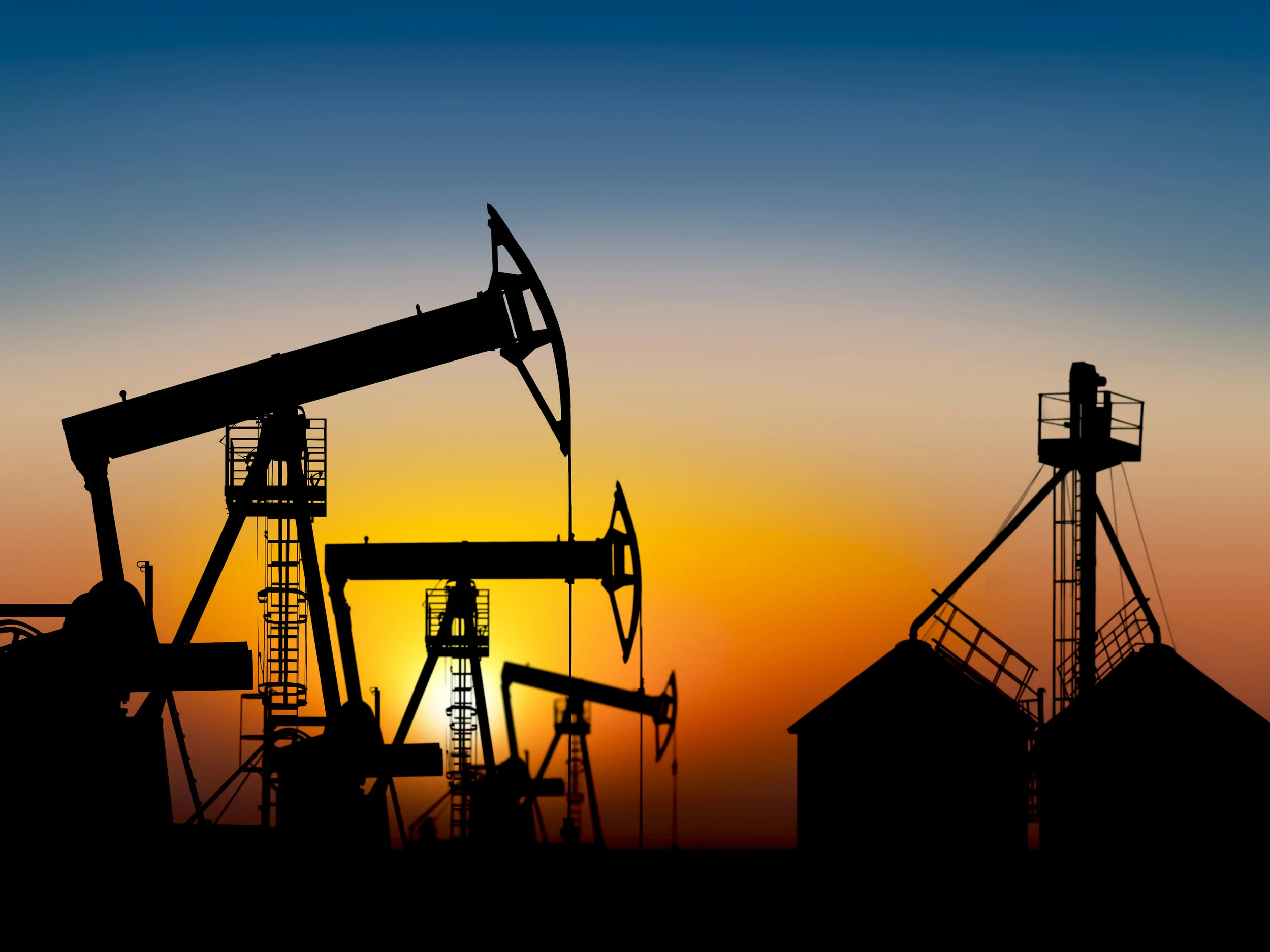
DIGITAL OILFIELD OPERATION
THE POTENTIAL CLIENT
An U.S.-based oil refinery employs about 1,000 workers in various types of hazardous locations where combustible materials are present. The company has begun the evolution to a “digital oilfield” operation, where advanced software and big data analysis helps to automate and improve the efficiency of business processes. The goal is to optimize cycle time and eliminate downtime, as well as improve decision-making and, ultimately, increase ROI and overall productivity.
THE CHALLENGE
Although the facility is moving toward full digitisation, there is one major problem: approximately 15% of the refinery’s workforce works in zones of the plant that are classified as UL913 Class I Division 1 hazardous locations, where combustible materials are constantly present and, thus, only specially certified electronic equipment is permitted. The remaining 85% of the workforce works in zones that are classified as UL913 Class I Division 2, where combustible materials are present only in the event of a fault in equipment. However, these Division 2 areas immediately become Division 1 if a leak or rupture causes flammables to escape an enclosure. And many employees move into and out of Division 1 areas at some point during their shift. Traditional devices, such as smartphones or tablets, cannot enter these Division 1 areas because they produce energy sufficient to cause a spark that could ignite the explosive atmosphere. Thus, workers in these zones are restricted to recording data with pen and paper and then later entering it into a desktop computer or other less-certified mobile device in a less-volatile zone of the plant. Unlike their colleagues in less dangerous areas who have replaced paper-based processes with digital reporting and communications, the Division 1 workers cannot receive nor transmit real-time information from within their work areas. The Division 2 workers who have begun to digitize their processes with corresponding certified mobile devices are limited in their mobility to only certain zones of the plant, plus they are running the risk of adding explosive potential to catastrophe should an emergency arise.
THE WISH LIST
Ideally, the Division 1 hazardous location workers would like to:
• Collect data and input it directly into their ERP system
• Send and receive emails via Microsoft Outlook, which is the company’s standard
• Access online company manuals and instructions via Microsoft Azure cloud
• Send photos and video to document inspections
• Communicate in real time with colleagues via an “augmented reality” solution, such as Skype for Business
• Open and close work orders
• Create timestamps and audit trails
• Generate Microsoft Word reports to share with teams
• Track inventory and order parts and materials easily and quickly
Although the plant is Wi-Fi equipped, all of the activities of Division 1 workers must be done by hand and then digitized later when they are outside of the hazardous location. Their technology disconnect causes a delay in action, creating lag time in decision making, which, in turn, leads to increased downtime and, hence, decreased productivity.
THE PROPOSED SOLUTION
The proposed technology solution for this oil refinery is two-fold:
1. Hardware that is suitable for every employee.
2. Software that allows every employee to access the same cloud-based services and information across the entire organization.
HARDWARE
The Aegex10 Intrinsically Safe Tablet is the ideal mobile device for this situation because it can be used by any worker in the facility, including those in the most explosive Division 1 areas, those who may enter into a Division 1 area on occasion, and everyone in the plant who will suddenly be in Division 1 in the event of an emergency.
Certified for UL913 Class I Division 1 hazardous locations, as well as equivalent areas in Europe (ATEX Zone 1) and internationally (IECEx Zone 1), the Aegex10 operates on Wi-Fi or 4GLTE from any hazardous location around the globe on a unified platform.
The 10.1-inch Windows-based tablet is rated IP65 rugged for industrial use, yet is lightweight and priced as low as non-certified devices. It’s Windows 10 operating system gives users uniform access to the Microsoft cloud, plus apps and services, including custom-designed software built by TAAP Limited.
“The Aegex10 IS Tablet brings the full power of Windows 10 and complementary apps directly into the most hazardous zones of industrial operations. With TAAP apps running on Aegex tablets, operators can quickly and easily capture, share and analyze data in real time directly from locations that were previously out of reach of modern communications.”
–Thomas Ventulett, Aegex CEO
SOFTWARE
TAAP can create custom applications for the refinery to help streamline business processes. The Aegex10 tablets can bring those apps directly into the areas where Division 1 workers need to use them.
TAAP can build a cloud-based solution on Windows Azure and digitize all of the company’s forms – work permits, work orders, maintenance records, etc. – to make them accessible to workers in any zone via the Aegex10 tablets. Using various TAAP apps on the Aegex tablets, workers monitoring Division 1 hazardous areas could take photos and videos, sign documents and annotate information with textbased descriptions. TAAPs reports can be generated directly from the Aegex10 as either Microsoft Word documents or PDF files and then emailed or saved. TAAP could create custom report templates with company branding and make each report specific to each project.
“TAAP works with global organisations to streamline their processes and drive efficiency, so having a suitable Windows 10 device such as the Aegex10 tablet to provide our applications means we can extend our reach into areas which were previously unsuitable for sending and receiving real-time data.”
–Steve Higgon, TAAP CEO
THE RESULTS
By implementing the electronic reporting solution proposed by Aegex and TAAP, the refinery would be able to:
• Visually and verbally share information from within Division 1 areas: Using Skype for Business or photos of inspection points taken and shared electronically, inspectors could collaborate in real time directly from Division 1 hazardous areas.
• Produce branded and advanced reports from complex data.
• Reduce time converting inspection data into written reports: Electronic reports could be created with a TAAP app and immediately converted into Microsoft Word documents to be edited in Word or Word Online on the Aegex tablets.
• Immediately share data, reports and ideas: Employees could use the same Microsoft tools as their rest of their organization worldwide, including Outlook, Yammer and other communications services to collaborate and share information. Data could be sent directly to other workers, into a secure web portal using Microsoft Azure, or into existing back-office databases.
• Access reports and other information offline. If the plant did not have Wi-Fi, the Aegex/TAAP solution could operate on 4G LTE. Or if no cloud connection was possible, all data captured by TAAP apps could be stored on the Aegex tablet for later transmission.
• Utilize secure storage and control access to reports: All reports and supporting audiovisual data could be stored in a Microsoft cloud portal hosted by Windows Azure to be accessible to authorized viewers.
• Backup and store large quantities of data with Azure.
• Integrate TAAP electronics reporting tools into existing workflow management system.
• Have access to TAAP customization, training and software support.
• Access Microsoft training and support.
• Download pre-configured forms from the Microsoft Store.